Reverse FMEA - A new and upcoming Customer Specific Requirement
For more than 60 years, Failure Mode and Effect Analysis has been used as an engineering development tool, to evaluate and mitigate risk in product and process designs. This tool has been used to thoroughly analyze potential design weaknesses and estimate failure frequency. Based on the preventative and detective controls, it facilitates decisions concerning the types of controlling actions that could be taken, and prioritizes actions based on the level of risk (APN or RPN). Through the Process FMEA, identified controls can be incorporated in the process to prevent or detect potential quality process concerns. These methods are then captured in the process or process efficiencies, control plans, and work instructions.
Recently, OEMs have identified in their IATF 16949 Customer Specific requirements, the need to Develop Reverse FMEAs. The purpose of the Reverse FMEA is to assure the customer that risks defined in the PFMEA are properly addressed and functioning as promised once the product goes into production. Even though the PFMEA is developed early in the production cycle, the verification of the effectiveness of identified controls is not always completed. This lack of verification may result in risk to the customer if the process design controls do not adequately provide the intended coverage. Additionally, potential issues may only become apparent after the product goes into production.
In basic terms, the Reverse FMEA (always centered on the PFMEA) is a focused review of the operation, to access controls identified in the approved PFMEA and testing to verify the ranking assigned for the various prevention and detection controls. It offers an opportunity for Subject Matter Experts to focus on a given operation and verify all failure modes, causes, and controls were identified in the original PFMEA. This must be done while the process is running at production cycle time and without disrupting production.
Author
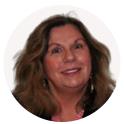
Mary Rowzee
Mary Rowzee is an Omnex consultant with extensive experience and achievements in Quality Systems development, implementation and auditing to ISO 9000 series and IATF 16949 standards; Six Sigma Black Belt Problem Solving and Advance Quality Tools including: Design and Process FMEA, Design and Process Verification and Test Planning, Complex Statistical Analyses and Reliability Prediction, Modelling and Risk Reduction. Mary is a writing member of AIAG-VDA FMEA 1st edition and the Core Tools Guidelines: SPC 2nd edition, MSA 4th edition, EFMEA 1st edition, PPAP 4th edition and APQP 2nd edition. Mary has been actively leading industry practices and application of ISO 26262 Functional Safety Standard for Electrical/ Electronic Products; Software FMEAs, ASPICE, CMMI and Quality; Supplemental Monitoring and Systems Response (MSR) FMEAs; Safety of the Intended Functionality (SOTIF) ISO 21448 and use of Safety Engineering tools (Reliability Block Diagrams, Hazard and Risk Analyses, Addressing ASIL rated risks) in Advanced Driver Assistance Systems (ADAS). She also served as GM Global representative on AIAG-VDA and SAE Quality Standards development teams.
Upcoming Webinar : From Spreadsheets to AI Agents: Unlocking the Power of AI for FMEA Development
Speakers:
Antony John
Date and Time:
Aug 14 2025 11:00AM Eastern Time (US and Canada)
RegisterUpcoming Webinar : Achieving Net Zero: How Standards Can Help
Speakers:
Chad Kymal, John Shideler
Date and Time:
Aug 26 2025 11:00AM Eastern Time (US and Canada)
RegisterUpcoming Webinar : The Intelligent Auditor: Empowered by AI & Your ultimate Problem Solver using AI
Speakers:
Andrei Samoila, Michael Popenas
Date and Time:
Aug 28 2025 11:00AM Eastern Time (US and Canada)
Register